All certifications
Guarantee and demonstrate the high quality of your products and services with certification to DIN EN ISO 9001.
Ensure quality through process optimization
In order to prevail in the face of global competition, high, consistent quality, customer satisfaction and well-functioning processes are essential. To meet these requirements, a reliable quality management system is needed. The quality management standard DIN EN ISO 9001 provides the basis for this, outlining the minimum requirements that a quality management system has to fulfill.
Introducing ISO 9001 not only enables you to improve the performance of your company in all areas, but also demonstrates your company’s high quality standards to internal and external stakeholders.
Advantages of certification to ISO 9001
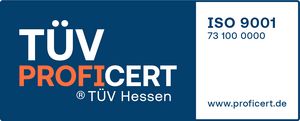
There are many good reasons for an ISO 9001 certification:
- Cost and time saving
- Increased process reliability within the company
- Definition and documentation for increasing legal certainty and efficiency
- Verifiable compliance with customer requirements
- Increased competitiveness
- Increased market acceptance
Process of certification to ISO 9001
Stage 1: readiness assessment
The certification begins with a readiness assessment. During this, the audit team determines which requirements of ISO 9001 are already met and where improvements are required.
Stage 2: audit
The readiness assessment is followed by the actual certification to ISO 9001 – the audit. The audit is divided into a documentation/process check and an on-site audit. In the first step, the auditor checks the documentation (process descriptions), focusing on compliance with the requirements set out in the standard. The second step takes place on the company’s premises. Here, the effectiveness of the QMS and the implementation of the requirements of ISO 9001 are checked and assessed. Deviations discovered during the audit can be corrected. Once the auditors have checked and approved the effectiveness of the corrective measures, you receive an audit report and, once the process has been approved, the certificate.
As part of the certification procedure – consisting of a readiness assessment and document inspection in advance and a subsequent on-site company audit – the following elements, among others, are tested and assessed:
- Context of the organization with specification of application area
- Management/policy
- Planning
- Support
- Operational realization
- Assessment of performance
- Improvement
How long is the certification valid?
The TÜV PROFiCERT certificate for DIN EN ISO 9001 is awarded upon successful completion of the certification process. It is valid for three years and must be confirmed every year by a monitoring audit. A re-certification is performed after three years.
Would you like further information or a meeting?
Then simply get in touch with us:
TÜV Hessen certification body
Robert-Bosch-Straße 16
D-64293 Darmstadt
Tel. +49 6151 600-331
Fax: +49 6151 600-336
Email: Contact